Application
Optimize tool and die setups with compression testing and matrix array sensors. Achieve even force distribution, reduce defects, and extend tool life.
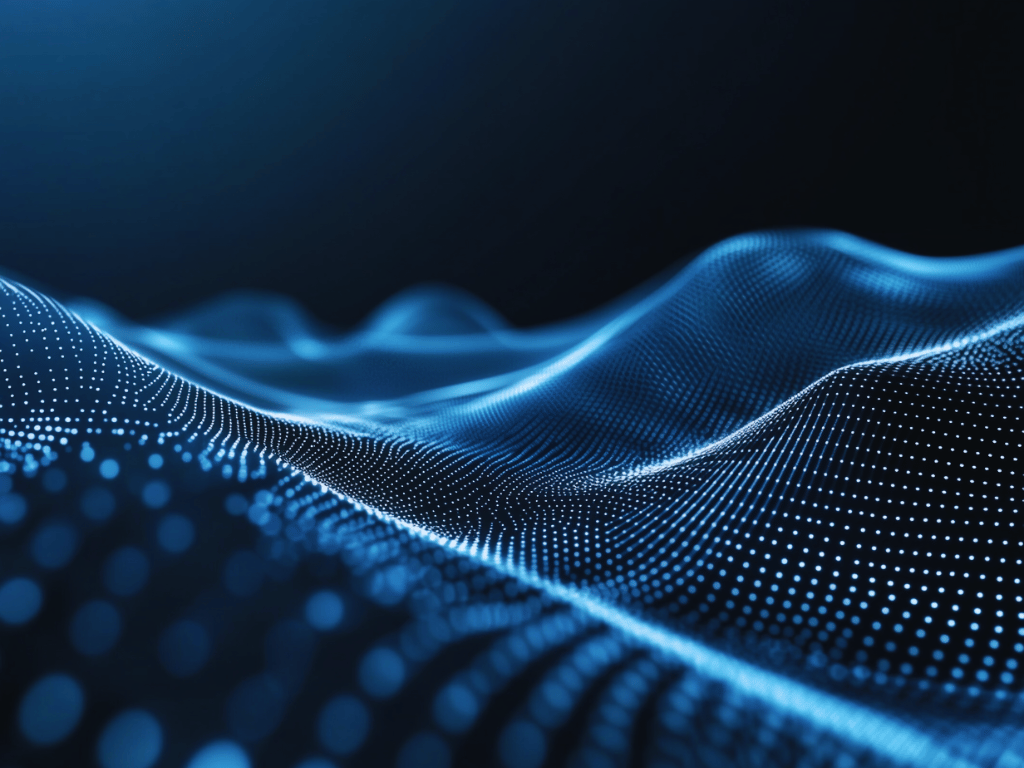
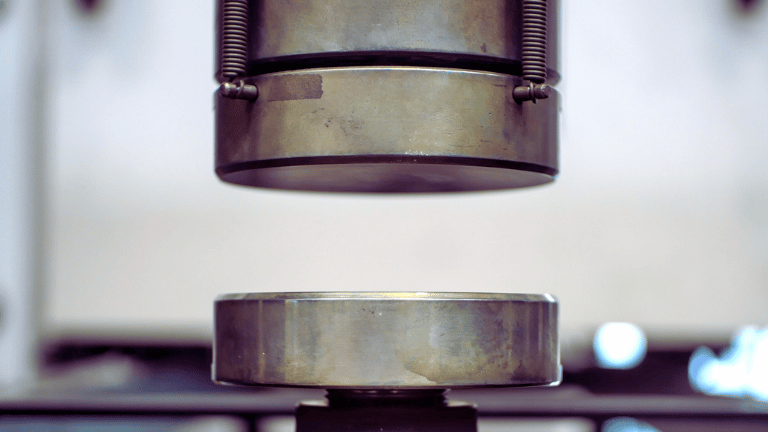
Enhancing Tool & Die Setup with Compression Testing and Matrix Array Sensors
Introduction
In high-precision manufacturing, tool and die setup is a critical factor that directly impacts product quality, production efficiency, and tooling longevity. Misaligned dies, uneven pressure distribution, and excessive wear can lead to defects, wasted materials, and costly downtime.
To address these challenges, manufacturers are increasingly integrating compression testing with matrix array sensors—a powerful solution that provides high-resolution pressure mapping, ensuring even force distribution across the die surface.
This article explores how matrix array sensors revolutionize compression testing in tool and die applications, providing engineers and manufacturers with real-time insights to optimize press alignment, enhance product consistency, and extend tool life.
Why Compression Testing is Crucial for Tool & Die Setup
1. Ensuring Even Force Distribution
In metal stamping, forging, and injection molding, dies must distribute force uniformly to prevent warping, burrs, cracks, or uneven material flow. Compression testing validates force application, helping engineers make necessary adjustments before production begins.
2. Extending Tool and Die Lifespan
Repeated stress on a misaligned or poorly calibrated die leads to premature wear and tool failure. Identifying high-stress areas through pressure mapping allows for preventive maintenance, reducing downtime and replacement costs.
3. Improving Production Efficiency
A well-calibrated tool setup results in higher yield rates, fewer defects, and minimized rework. By using real-time compression data, manufacturers can fine-tune tooling conditions and achieve optimal performance.
4. Reducing Maintenance and Downtime
Early detection of uneven pressure points prevents severe tool damage, reducing unexpected machine breakdowns and costly production stoppages.
How Matrix Array Sensors Improve Compression Testing
Traditional single-point load cells provide limited data on force distribution, making it difficult to diagnose localized pressure imbalances. In contrast, matrix array sensors capture high-resolution, multi-point pressure data across the die surface, offering a complete picture of force application.
Key Advantages of Matrix Array Sensors in Compression Testing
- Full-Surface Pressure Mapping – Unlike conventional sensors that measure force at a single point, matrix array sensors capture a detailed force distribution profile, allowing for comprehensive die alignment verification.
- High-Resolution Data for Precise Adjustments – The grid-based sensor structure ensures that even the smallest misalignment or uneven force application is detected and corrected.
- Real-Time Feedback for Immediate Corrections – Engineers can analyze force data in real-time, making on-the-spot adjustments to optimize press alignment and improve part consistency.
- Prolonged Die and Tool Longevity – By ensuring even force application, manufacturers reduce localized stress concentrations, which can weaken tools over time.
Step-by-Step: Implementing Compression Testing with Matrix Array Sensors
1. Position the Sensor in the Press Setup
Place the matrix array sensor between the press and the die to capture real-time force distribution data.
2. Apply Incremental Load Testing
Gradually apply force during test cycles to identify pressure imbalances before full-scale production begins.
3. Analyze Pressure Data and Identify Misalignments
Review detailed force distribution maps to pinpoint areas where pressure is too high or too low, which may indicate die misalignment or tooling defects.
4. Adjust Tooling or Press Alignment
Based on the pressure readings, fine-tune the press force, clamping pressure, or die positioning to achieve even force distribution.
5. Validate and Re-Test
Run additional compression tests to ensure that adjustments lead to optimized force application and defect reduction.
Applications of Compression Testing in Tool & Die Setup
1. Metal Stamping & Forging
Challenge: Uneven force distribution can lead to cracks, warping, and excessive material waste.
Solution: Matrix array sensors detect high-stress areas on stamping dies, allowing engineers to adjust force application for uniform pressure distribution.
2. Plastic Injection Molding
Challenge: Inconsistent clamping force results in flash, sink marks, and uneven thickness in molded parts.
Solution: Compression testing ensures even force application across the mold, reducing part defects and extending mold lifespan.
3. Research & Development for Die Optimization
Challenge: Developing new dies or tooling methods often involves trial-and-error, increasing costs.
Solution: Matrix array sensors accelerate die development by providing detailed force mapping, leading to faster design validation and reduced prototyping costs.
Conclusion
Compression testing with matrix array sensors is transforming the way manufacturers optimize tool and die setups, ensuring even force distribution, longer tool life, and higher production efficiency.
By leveraging high-resolution pressure mapping, engineers and production teams can fine-tune die alignment, reduce defects, and improve overall manufacturing quality.
Looking for precision force mapping solutions? Ceradex’s matrix array sensors provide the real-time pressure insights you need to elevate your tool & die performance.
Latest Insights
Collaboration Begins Here.