產業應用
探索如何利用FSR壓力矩陣感測進行壓力分佈量測,協助驗證電動車(EV)電池設計,進一步提升穩定性、耐用性及組裝品質。
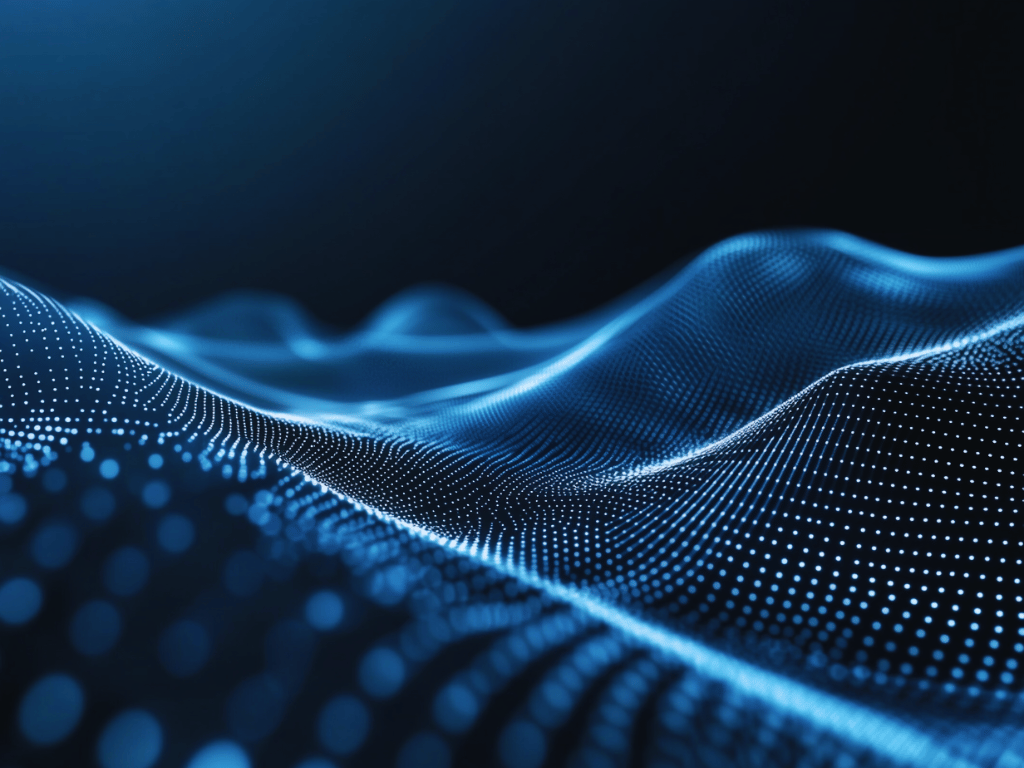
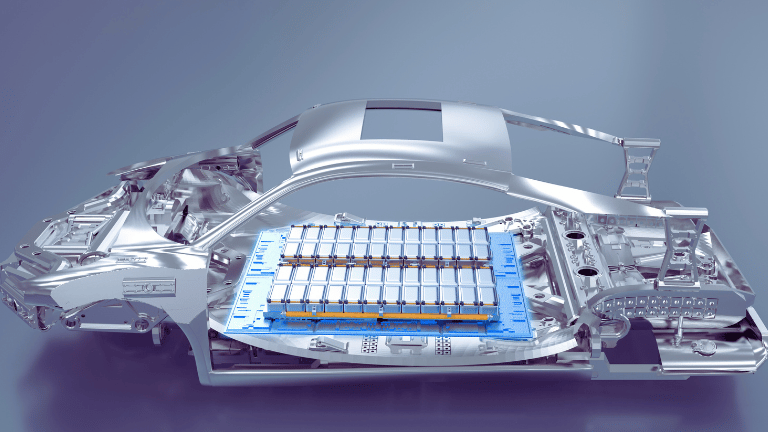
了解壓力分佈與FSR技術在電動車電池設計驗證中的應用
前言
隨著電動車(EV)邁入量產階段,電池設計所面臨的挑戰也日益複雜。如今的重點不再只是追求高容量和快充速度,結構穩定性與耐久性也變得同樣重要。
其中一個越來越受關注的議題,就是電池模組內部的壓力變化。壓力變化可能影響電芯之間的貼合緊密度、熱能傳導效率,甚至影響時間使用下的密封性與結構強度。
為了支援電池設計的驗證工作,部分研發團隊開始導入壓力分佈量測技術,搭配客製化的FSR(力敏電阻)矩陣。這些柔性感測層可在產品開發與測試階段暫時安裝,用來觀察壓力的分佈和變化。雖然這類感測器不會留在最終產品中,但卻能在設計驗證階段提供關鍵資訊,有助於提升組裝品質與整體可靠性。
透過壓力分佈技術,掌握電池設計與驗證的關鍵細節
1. 充放電週期中的壓力變化
鋰電池在充放電過程中會出現輕微的膨脹與收縮。雖然這些變化幅度不大,但隨著時間累積,可能導致以下問題:
- 電芯出現位移或排列不整齊
- 壓力集中於電池外殼,影響結構強度
- 熱傳導路徑產生變化,影響散熱效能
若能在電池模組設計驗證階段,於原型中暫時安裝超薄型 FSR(力感測電阻)壓力矩陣感測,就能在模擬真實使用情境下,即時觀察這些細微的壓力變化。
這些第一手的量測數據,有助於工程團隊進行以下優化:
- 調整電池外殼的剛性或加強支撐設計
- 改善熱管理與散熱配置
- 提前掌握並排除可能導致結構損壞的壓力問題
與其僅依賴電腦模擬,導入FSR壓力感測技術能提供更貼近實際操作條件的驗證依據,進一步提升電池的穩定性與耐用性。
2. 環境耐久測試中的壓力觀測
在實際駕駛環境中,電池模組需要承受來自各種外部條件的挑戰,例如撞擊、振動、水花衝擊與空氣動力產生的壓力。隨著時間累積,這些外部壓力可能導致:
- 電池外殼出現裂縫或變形
- 密封結構遭到破壞,導致水氣或灰塵侵入
- 結構部位產生疲勞裂痕或損壞
在環境模擬測試中,可透過鋪設FSR壓力感測墊,記錄如路面碎石撞擊、高壓清洗等模擬情境下的壓力分佈情況。
這些數據可幫助工程師:
- 強化強化高應力集中或反覆受力的結構區域
- 選用更堅固或具彈性的外殼材料
- 優化保護機構設計,提升整體耐久性
透過壓力分佈圖像,研發團隊能更具體地辨識弱點區域,進一步優化電池模組的結構與可靠性設計。
3. 模組組裝過程中的壓力均勻性
在電池模組的組裝階段,確保壓力分佈均勻是維持長期性能的關鍵。如果壓力施加不均,可能導致:
- 電芯之間的電氣接觸不良
- 在振動或熱循環下,更容易發生損壞
- 模組品質不穩定,導致良率下降
透過在早期組裝驗證階段導入FSR感測層,可即時監控每顆電芯所受到的壓力分佈情況,確認是否壓力一致。
這有助於:
- 微調壓裝設備的參數設定
- 降低電芯變形或組裝缺陷的風險
- 提升整體製程的一致性與可控性
將FSR應用於實際組裝壓力驗證,不僅能提升品質控制,也強化了產品在量產過程中的可靠性。
結論
雖然FSR矩陣感測不會出現在最終的電池產品中,但它在研發與驗證階段扮演了不可或缺的角色。從充放電反應、外部衝擊到組裝壓力,這些實測的壓力分佈數據,讓工程團隊能夠及早發現潛在問題,並持續優化設計。
隨著EV電池朝向更高能量密度與更精密結構發展,導入壓力感測技術將不再只是選項,而是確保品質、耐用性與安全性的必要手段。
最近更新
Collaboration Begins Here.