Glossary
Explore how screen printing powers innovations in electronics manufacturing, offering precision and versatility for high-volume production.
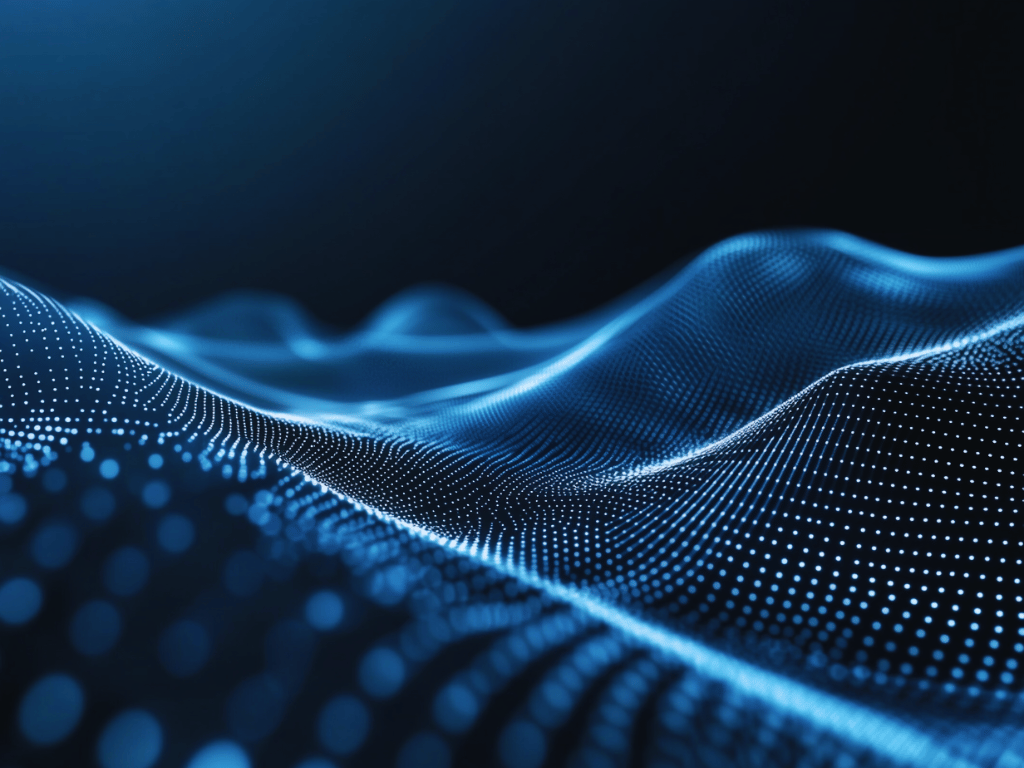
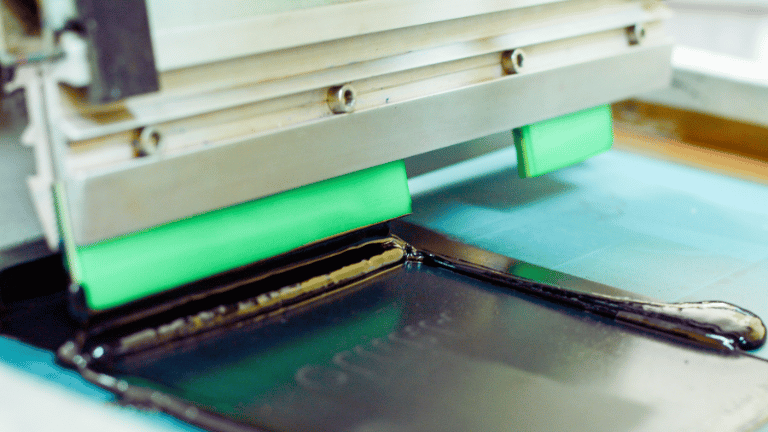
Precision Screen Printing: Process and Applications
Screen printing is a cornerstone technology in the printed electronics industry, providing a reliable and versatile method for creating electronic components such as circuits, sensors, and displays. This process involves transferring specialized conductive, dielectric, or resistive inks onto a substrate through a fine mesh screen and stencil, ensuring precise pattern control and uniform thickness. It is widely regarded as an efficient and scalable method for high-volume production, adaptable across various materials and industries.
The Screen Printing Process
Preparation of the Screen
- A fine mesh screen, typically made of polyester or stainless steel, is tightly stretched over a frame.
- A stencil is applied to block areas where ink should not pass through. Photographic techniques involving light-sensitive emulsions are often used to create these stencils.
Ink Application
- Specialized inks, such as conductive, dielectric, or resistive inks, are selected based on the application.
- These inks often incorporate materials like silver, carbon, or polymer composites to achieve the desired electrical properties.
- A squeegee pushes the ink through the open areas of the screen, transferring it onto the substrate below.
Printing
- The substrate—a flexible or rigid material like plastic films, paper, or glass—is positioned beneath the screen.
- The squeegee moves across the screen, depositing the ink in the desired pattern.
Curing
- Printed inks require curing to adhere properly and achieve the necessary properties. Methods include:
- Thermal curing
- UV curing
- Sintering
Advantages of Screen Printing in Electronics
Cost-Effective for High-Volume Production
Screen printing's scalability and low material wastage make it an economical choice for producing large quantities.
Versatility
The process supports a variety of substrates, enabling applications in flexible electronics, wearable devices, and more.
Precise Thickness Control
Screen printing ensures accurate control over ink layer thickness, which is essential for applications requiring uniform performance.
Pattern Accuracy
This method achieves intricate and detailed patterns, meeting the demands of advanced electronic designs.
Key Applications of Screen Printing
- Flexible Circuits
- Enables the production of circuit boards that can bend and flex without breaking.
- Wearable Electronics
- Ideal for printing sensors and circuits on flexible substrates, integrating seamlessly into garments and accessories.
- Solar Panels
- Used for depositing conductive patterns on solar cells, enhancing efficiency and energy output.
- Displays
- Plays a critical role in producing OLED and other types of electronic displays.
- Medical Devices
- Used to print biosensors and components for diagnostic and monitoring equipment.
Conclusion
Screen printing is a critical process in modern manufacturing, especially within the printed electronics industry. Its scalability, versatility, and precision make it indispensable for creating innovative and cost-effective electronic components. From flexible circuits to medical devices, this process continues to enable advancements across various industries.
Latest Insights
Collaboration Begins Here.