Application
Discover how force sensing resistors improve tactile sensing in humanoid robots, enabling safer object handling, precise grip control, and stable walking.
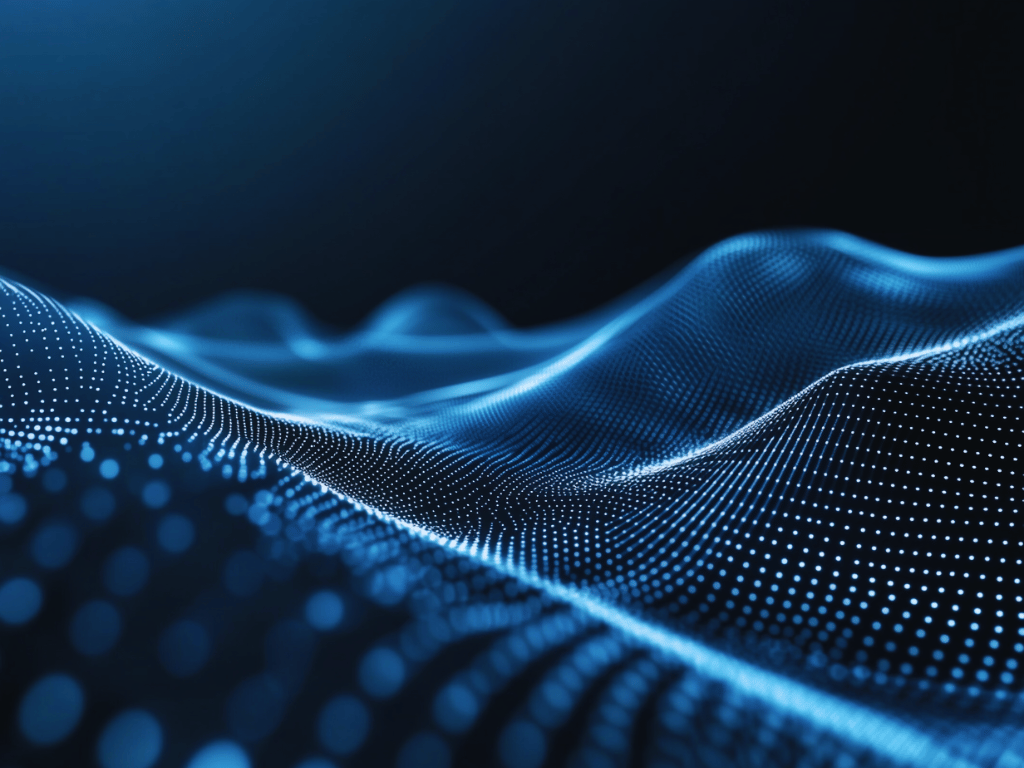
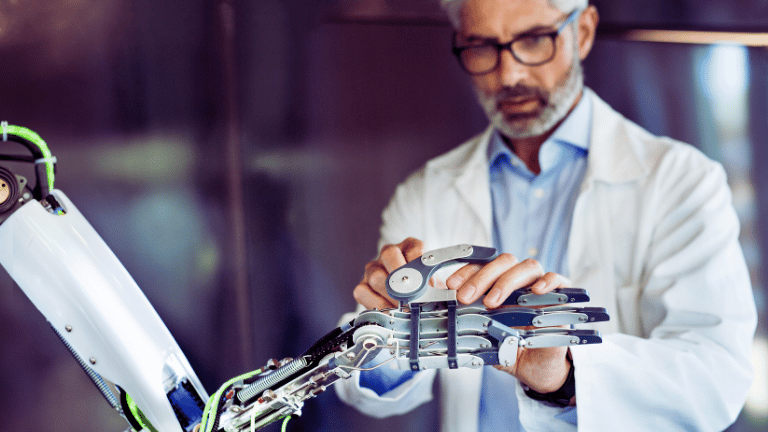
Enhancing Humanoid Robotics with Force Sensing Resistors
Introduction: Tactile Sensing – A Core Challenge for Humanoid Robotics
As humanoid robots continue advancing, their ability to physically interact with objects and people becomes increasingly important. One essential aspect of this interaction is tactile sensing, which allows robots to detect and respond to physical contact.
Force Sensing Resistors (FSRs) offer a lightweight and adaptable sensing solution, making them particularly well-suited for humanoid robots requiring real-time force feedback in hands, feet, or body surfaces. This article explores the practical application of FSR technology in humanoid robotics, with realistic assessments of its benefits, challenges, and considerations.
Understanding the Role of FSR in Tactile Sensing
Tactile sensing in humanoid robots demands sensors that are:
- Thin and lightweight to preserve dexterity.
- Flexible to conform to curved surfaces like robotic fingers.
- Customizable to detect subtle or strong forces as needed.
- Responsive in real time for dynamic grip adjustment and safe interaction.
Force Sensing Resistors meet these requirements through their unique structure — a thin, polymer-based sensor whose resistance changes when force is applied. This simple yet effective mechanism enables direct measurement of contact force, making FSR a preferred choice for integration into robotic skin, fingertips, and foot sensors.
Key Benefits of FSR Technology for Humanoid Robots
1. Seamless Integration into Complex Forms
Humanoid robots require sensors that can conform to curved or irregular surfaces, especially in areas like hands or soles of the feet. FSRs can be produced as thin, flexible sheets that are easily embedded into artificial skin or integrated into existing joint designs without adding significant bulk.
2. Tailored Sensitivity for Task-Specific Performance
Grasping a fragile object like a test tube requires vastly different force sensing than holding a tool firmly. FSRs can be customized to match these force ranges, ensuring the robot can detect both light contact and firm pressure using the same sensing platform.
3. Real-Time Force Feedback for Adaptive Control
In tasks like object manipulation, humanoid robots must continuously adjust grip strength based on surface texture, object weight, and unexpected disturbances. FSRs offer fast response times, enabling immediate feedback to the robot’s control system, allowing for adaptive grip adjustments in real-time.
4. Lightweight Construction Preserving Mobility
The compact form factor of FSRs ensures they do not hinder the robot’s mechanical flexibility or mobility. In humanoid feet, for example, FSRs can be applied as thin sensing pads without compromising gait or foot articulation.
Real-World Applications in Humanoid Robotics
Tactile Fingers for Object Manipulation
Embedding FSRs into robotic fingertips enables detection of contact forces when grasping objects. This data helps the robot balance grip strength—applying enough force to hold the object, but not so much that fragile items break.
Foot Force Sensing for Balance and Gait
Bipedal robots rely heavily on foot sensors to monitor ground contact and balance. FSRs positioned under the sole can measure distributed forces across different foot zones, aiding in stable walking, dynamic balancing, and terrain adaptation.
Whole-Body Contact for Human Interaction
In collaborative scenarios where robots work alongside humans, distributed FSR arrays across the robot’s surface can detect unintentional contact, enabling safer and more responsive physical interaction.
Challenges to Consider When Using FSR in Robotics
While FSR technology offers clear benefits, realistic implementation requires addressing these factors:
- Calibration Complexity: FSR output is non-linear, requiring tailored calibration algorithms to ensure accurate force estimation across different surfaces and materials.
- Long-Term Stability: Extended use can lead to slight sensitivity drift, making periodic recalibration necessary for precision-critical applications.
- Environmental Protection: In outdoor or high-contact environments, FSRs may require protective overlays to shield against moisture, dust, or abrasion.
Combining FSR with Other Printed Sensing Technologies
FSRs are just one part of the sensing puzzle in humanoid robots. By utilizing screen printing technology, multiple functional layers can be combined into a single, custom-configured sensor array, providing advanced tactile and environmental sensing capabilities.
Alongside force sensing, screen-printed sensors can also incorporate:
- Temperature sensors to monitor surface and environmental heat.
- Moisture sensors to detect liquid contact—valuable for service robots in kitchens, healthcare, or outdoor use.
- Printed heaters to generate warmth, enhancing user comfort during physical interaction in caregiving or personal assistance roles.
This multi-sensor fusion approach—enabled through a unified printing process—allows developers to design thin, flexible, and fully integrated sensing surfaces, enhancing both functionality and real-time responsiveness when robots operate in unstructured, real-world environments.
Final Thoughts
Force Sensing Resistors offer a mature, reliable, and adaptable solution for enhancing tactile sensing in humanoid robots. Their combination of flexibility, real-time response, and customizable sensitivity makes them especially valuable in robotic hands, feet, and artificial skin.
As humanoid robots continue to expand into healthcare, service, manufacturing, and personal assistance roles, practical, cost-efficient tactile sensing technologies like FSR will remain a key enabler of safe and capable physical interaction.
Latest Insights
Collaboration Begins Here.